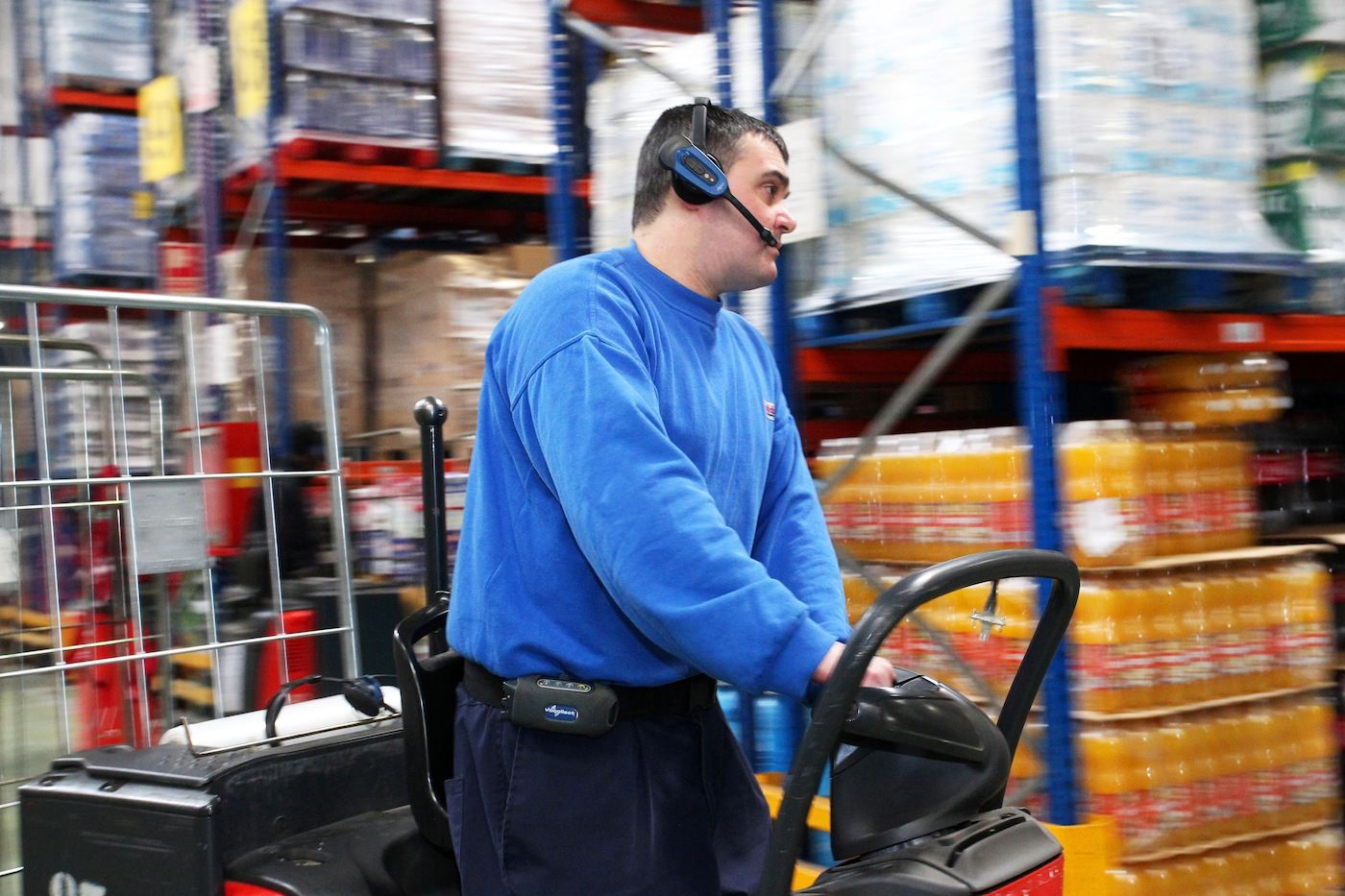
Sorli Discau ha desarrollado su propio sistema de voz con Vocollect VIO en su almacén principal de 20.000 m² ubicado en Granollers-Montmeló, Barcelona. La compañía gestiona en esta plataforma diariamente 12.000 palets, 200 camiones y 5.700 referencias, con 62 trabajadores de los que 18 utilizan las soluciones de Vocollect.
Antes de la nueva instalación del sistema de voz, el almacén contaba con un sistema de radiofrecuencia y un SGA propio hecho a medida y desarrollado internamente en su totalidad, con el cual se realizaban los pedidos mediante papel. La empresa buscó entonces un sistema con el que poder compartir todos los métodos de preparación.
La decisión de implementar Vocollect Voice se tomó después de estudiar los procesos con el objetivo de encontrar una solución que aumentara la productividad y mejorara las condiciones de trabajo.
La solución
El departamento de sistemas, junto con los responsables del almacén, llevaba tiempo buscando una solución que permitiera mejorar los procesos logísticos y de almacenamiento aumentando la productividad de los trabajadores.
Una vez optaron por implementar la tecnología Vocollect Voice, escogieron empezar por la sección de refrigerados porque los trabajadores de esa área utilizaban un terminal de mano que les impedía aumentar su productividad. La opción de integración mediante VIO (Vocollect Interface Object) daba más libertad en el desarrollo.
Este sistema daba la posibilidad de desarrollar el sistema de voz sin depender de nadie, "todo el desarrollo es propio porque nosotros siempre hemos preferido hacerlo vía appis, directamente con conectores tipo “socket” y cuando vimos que con VIO era posible no tuvimos dudas, nos permite una relación directa con cada terminal de voz”, señalan desde Sorli Discau.
Aumento de la productividad del 12%
Después de un periodo de desarrollo de tres meses para poner en funcionamiento una parte del almacén, el que corresponde a la de los productos de charcutería, se decidió ampliar el uso de la voz al resto de la plataforma.
Entre los resultados obtenidos con esta solución destaca un aumento de la productividad de un 12%, llegando al 20% en el picking, con una consecuente mejora del servicio a tiendas y clientes entorno al 7%. El beneficio principal ha resultado también a nivel de riesgos laborales de los trabajadores ya que al trabajar con las manos libres, se han reducido mucho las incidencias.
Por otro lado se ha reducido el tiempo de formación de cuatro días a 24 horas, el tiempo necesario ahora para tener un preparador plenamente preparado, con lo que se amplía la capacidad de reacción ante picos de trabajo.
Además, las incidencias en periféricos y elementos propios de los equipos se han reducido drásticamente disminuyendo los gastos de mantenimiento de los equipos en un 30%.