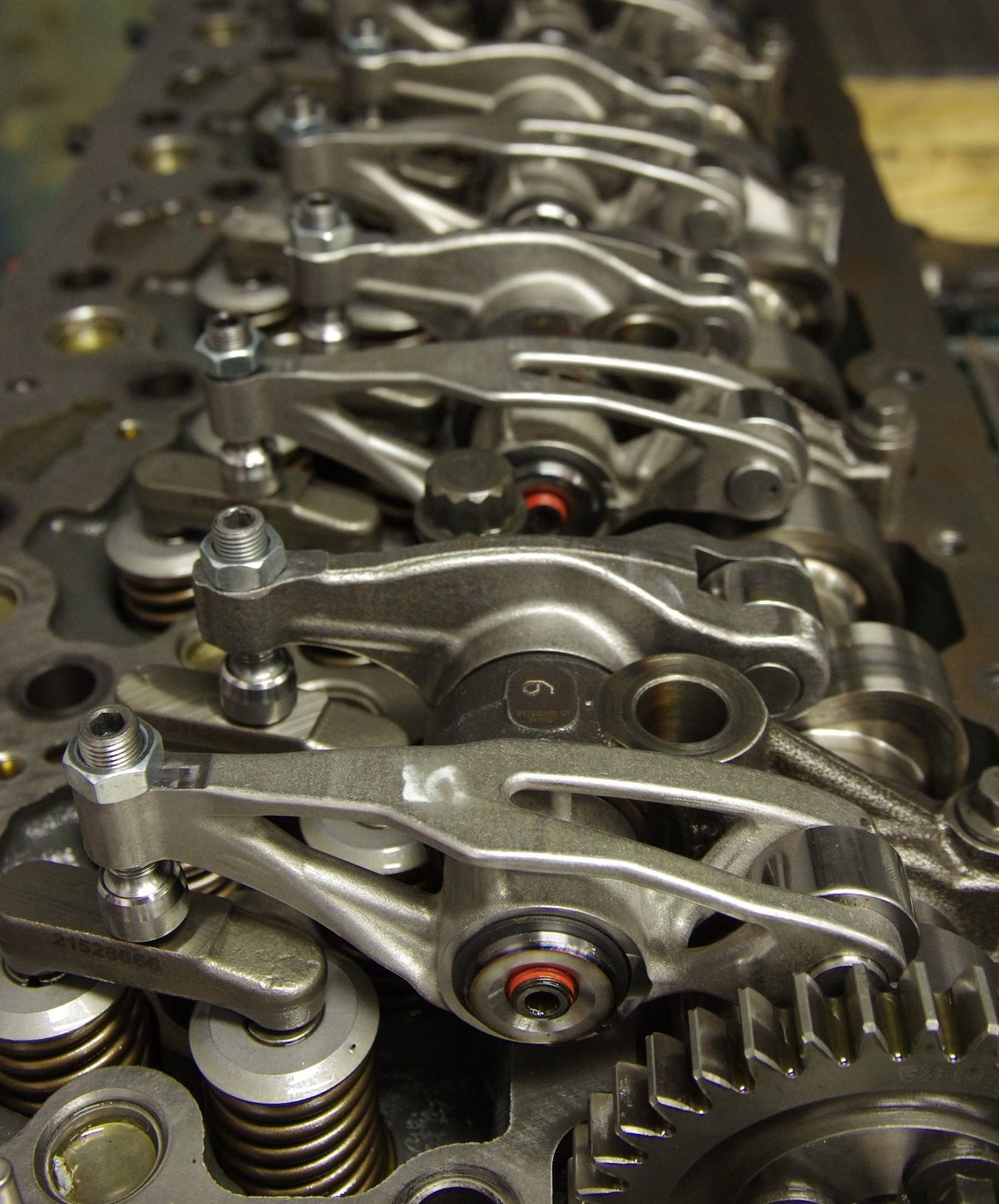
Renault Trucks ha incorporado la impresión 3D en metal en el proceso de fabricación de piezas con el fin de mejorar las prestaciones de los motores.
El fabricante ha conseguido diseñar un prototipo de motor DTI 5 de cuatro cilindros Euro 6 Step C, en el que ha incorporado la impresión 3D para la fabricación de los balancines y sus soportes. De esta forma, ha conseguido reducir en 120 Kg el peso de un motor de cuatro cilindros, y los ha probado con éxito con un motor Euro 6 en un banco de pruebas durante 600 horas.
Para la construcción de estas piezas, Renault Trucks ha utilizado el sistema de fabricación aditiva en metal, que funciona por acumulación de materia capa a capa, permite realizar formas complejas. También se ha conseguido optimizar el dimensionado de las piezas y reducir el número de operaciones de ensamblaje y, por tanto, reducir el número de componentes de un motor.
Esta nueva técnica abre nuevas perspectivas de desarrollo para los motores térmicos, ya que permite diseñar equipos más funcionales, más ligeros y con prestaciones óptimas.
En este caso, el número de componentes del motor DTI 5 se ha reducido en un 25%, con lo que se han utilizado 200 piezas menos en su fabricación.
Para los transportistas, la impresión 3D en metal mejorará el coste total de explotación de sus vehículos, ya que la disminución de la masa del motor permitirá más carga útily un menor consumo de carburante.
A corto plazo, este procedimiento de fabricación podrá utilizarse para aplicaciones muy específicas o para series cortas, según el fabricante.